The German parts manufacturer Mahle, industrial machine manufacturer Trumpf, and automaker Porsche have 3D printed pistons for the well-known 911 GT2 RS that are not only stiffer but also lighter. They have also integrated and closed the cooling duct in the piston crown, thus enhancing its power and efficiency.
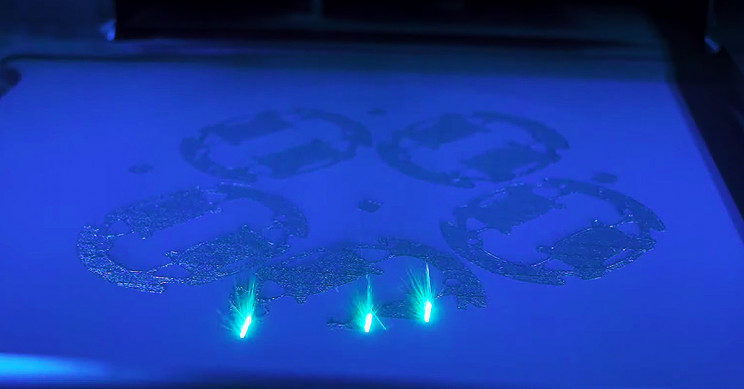
These 3D printed pistons will not be entering production any time soon since the piston crew feature cannot be reproduced via the conventional manufacturing methods. However, it should be noted that they do offer mechanical benefits since they weigh 10% less than the forged ones. These features, including the likes of reduction in weight and temperature, can help generate an extra 30 horsepower apart from the 700 horsepower that GT2 RS is already capable of generating.
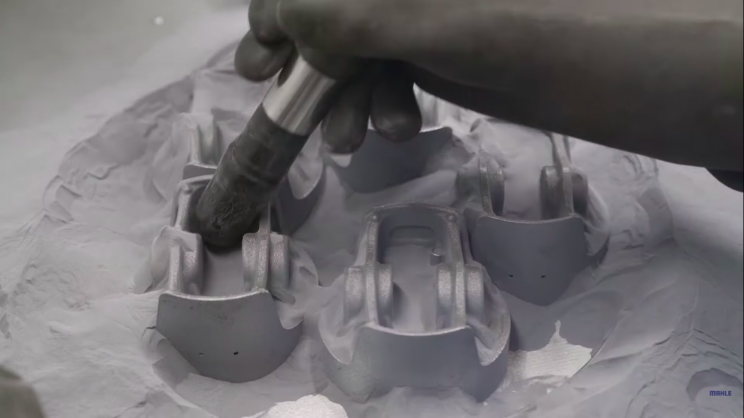
The 3D printed pistons have been created using the high-purity metal powder and relied on a laser metal fusion process for its creation. This means that it has been created using a laser beam that heats and then melts metal powder until the required shape is achieved. Once the desired shape has been achieved, the product undergoes validation by making use of measurement technology from Zeiss. Zeiss is a German optics company that is known for its camera lenses.
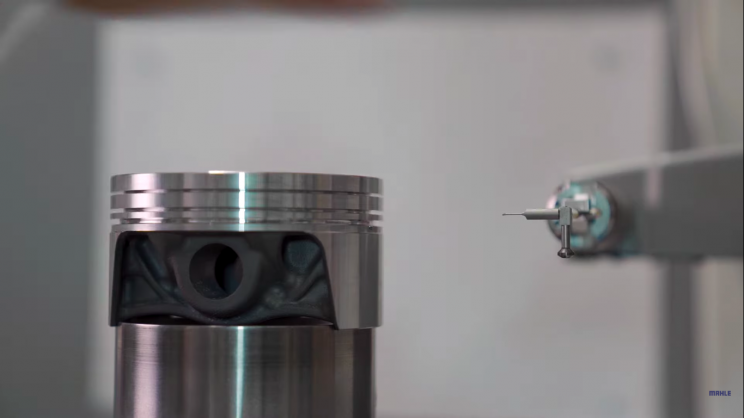
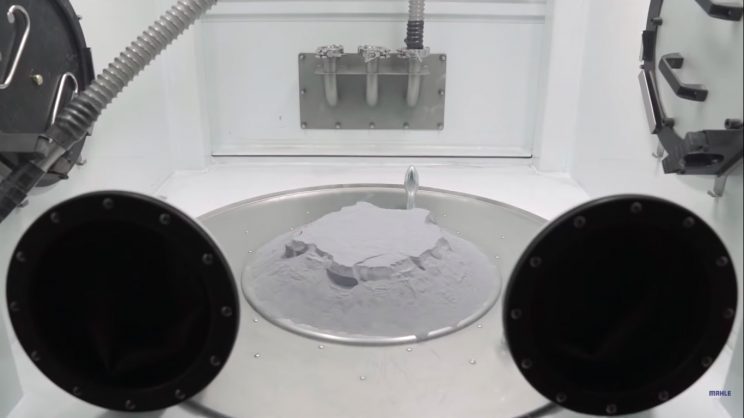
The 3D printed pistons were then analyzed for any defects and were placed on an engine test bench. They also underwent a 200-hour endurance drive simulation without any hiccups. Porsche senior engineer Frank Ickinger said, ‘Thanks to the new, lighter pistons, we can increase the engine speed, lower the temperature load on the pistons, and optimize combustion. This makes it possible to get up to 30 HP more power from the 700 HP bi-turbo engine, while at the same time improving efficiency.’
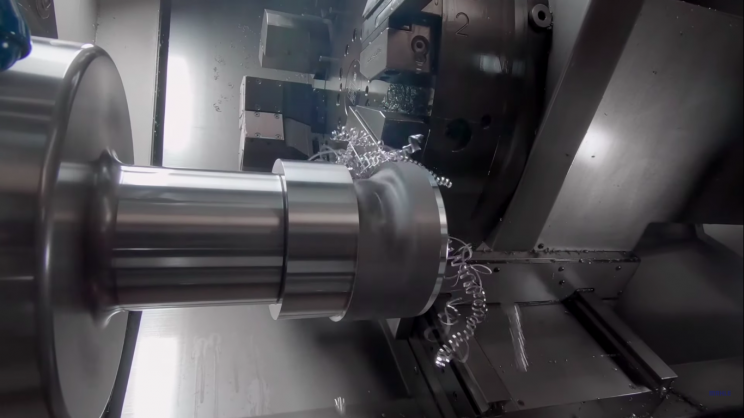
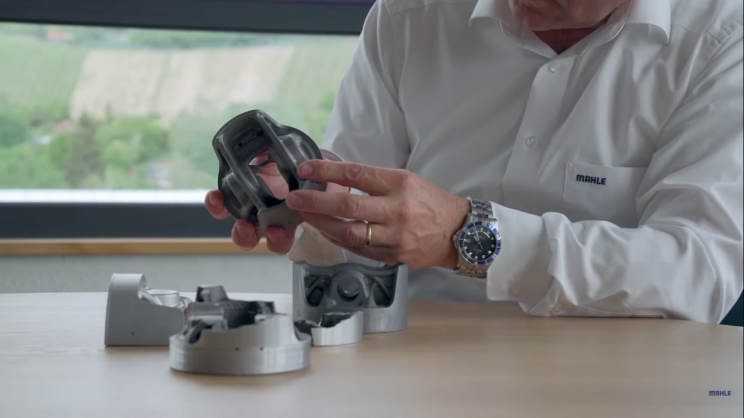
We’ll have to wait and see, however, when 3D printing becomes a norm for the regular vehicles.
Comments
Post a Comment
Tell us what you think